In the vast system of industrial production, slitting machines are extremely crucial equipment, widely used in various industries. They are tasked with precisely cutting wide materials into specific specifications to meet the actual needs of different production processes. Automatic servo two-way slitting machines and automatic two-way cardboard slitting machines are typical representatives in this regard. Although both have the function of two-way slitting and may look similar in appearance, they actually differ significantly in technical principles, performance, and applicable scenarios. A comprehensive and in-depth analysis of these differences is of great significance for enterprises to make accurate selections during equipment procurement, thereby effectively improving production efficiency and optimizing product quality.
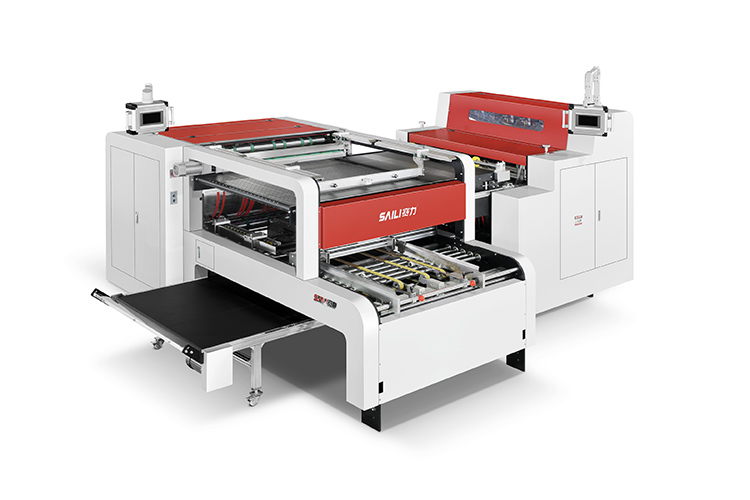
Ⅰ.Working Principles: The Essential Differences Driven by Technology
- Automatic servo two-way slitting machines are the crystallization of modern advanced technology. Their core power comes from servo motors, and the servo control system precisely regulates the motor's running speed, position, and torque. During the actual slitting operation, this system can flexibly adjust the position of the cutting tool and the cutting speed with high response speed and accuracy according to the preset parameters. For example, when slitting flexible materials such as films and papers, the system will monitor the tension changes of the materials in real time and quickly instruct the servo motor to make corresponding adjustments to ensure that the edges of the cut materials are smooth and flawless, fully meeting the strict requirements of high-precision production.
- Automatic two-way cardboard slitting machines, on the other hand, follow the traditional mechanical transmission principle. They mainly rely on motors to drive mechanical transmission components such as gears and chains to achieve the stable movement of the cutting tool in the horizontal and vertical directions. When cutting cardboard materials that are hard and thick, high-speed rotating cutting tools are used. Although this mechanical structure is highly stable during operation, due to the inherent clearance and friction in mechanical transmission, there are indeed certain limitations in the control of slitting accuracy compared with automatic servo two-way slitting machines. However, for some cardboard processing tasks that have relatively loose requirements for accuracy and pay more attention to cutting efficiency and equipment durability, automatic two-way cardboard slitting machines can complete the work excellently with their simple and reliable mechanical structure and powerful cutting power.
Ⅱ.Application Scenarios: Precisely Meeting Industry Demands
-
Automatic servo two-way slitting machines, with their high precision, high speed, and flexible control performance, hold an important position in industries with extremely high requirements for material slitting accuracy. In the electronic manufacturing industry, the slitting size accuracy of the insulating films used in the production of circuit boards is directly related to the electrical performance and stability of the circuit boards. Automatic servo two-way slitting machines can accurately slit the films into the required sizes, ensuring the reliability of product quality. In the optical film manufacturing industry, when producing key optical materials such as polarizing films for liquid crystal displays, the requirements for slitting accuracy even reach the extremely high standard of micrometers. Automatic servo two-way slitting machines can fully meet this challenge with their excellent performance.
- Automatic two-way cardboard slitting machines are mainly used in the packaging, printing and other industries. In the packaging industry, when mass-producing packaging products such as cartons and paper boxes, it is necessary to quickly slit large-format cardboard into small pieces of various specifications. These application scenarios have relatively low requirements for the slitting accuracy of cardboard, but put forward high requirements for slitting efficiency and the continuous working ability of the equipment. Automatic two-way cardboard slitting machines can efficiently complete the cardboard slitting task with stable speed and reliable performance, meeting the large-scale and high-efficiency production needs of the packaging industry. In the printing industry, when providing cardboard of different specifications for printing machines, automatic two-way cardboard slitting machines can also give play to their advantages of high-efficiency slitting to ensure the smooth progress of printing production.
Ⅲ.Performance Characteristics: A Comprehensive Comparison
- Slitting Accuracy: Relying on advanced servo control technology and high-precision transmission components, automatic servo two-way slitting machines can usually achieve a slitting accuracy of ±0.1mm or even higher, making them more than capable of handling materials with extremely high accuracy requirements. In contrast, limited by the mechanical transmission characteristics, the slitting accuracy of automatic two-way cardboard slitting machines is generally around ±0.5mm. This is acceptable in some cardboard processing scenarios with low accuracy requirements, but it falls short in operations with high accuracy requirements.
- Slitting Speed: In terms of slitting speed, automatic servo two-way slitting machines show obvious advantages. Their maximum slitting speed can reach hundreds of meters per minute or even higher, which can fully meet the high-efficiency needs of material slitting in high-speed production lines. Due to the physical characteristics of cardboard itself, too fast cutting speed of automatic two-way cardboard slitting machines can easily lead to increased tool wear and decreased cutting quality. Therefore, their slitting speed is relatively slow, generally about tens of meters per minute.
- Equipment Cost: Due to the adoption of advanced servo technology and a large number of high-precision components, the equipment cost of automatic servo two-way slitting machines is relatively high, which may be a great investment pressure for some enterprises with limited budgets. The structure of automatic two-way cardboard slitting machines is relatively simple, mainly relying on traditional mechanical transmission components, and the equipment cost is relatively low. For enterprises with tight funds and small production scales, it is a more cost-effective choice.
- Maintenance Difficulty: The maintenance of automatic servo two-way slitting machines is relatively complex and requires professional technicians to have the ability to regularly maintain and troubleshoot servo control systems, motors and other key components. Once a failure occurs, due to the complexity of its technology, the maintenance difficulty is high and the maintenance cost is relatively high. The mechanical structure of automatic two-way cardboard slitting machines is relatively intuitive and simple. The maintenance personnel within the enterprise can master the daily maintenance and repair skills of common faults after certain training, and the maintenance cost is relatively low.
In conclusion, automatic servo two-way slitting machines and automatic two-way cardboard slitting machines differ significantly in working principles, application scenarios and performance characteristics. When selecting equipment, enterprises must closely consider their actual production needs, product characteristics, budget constraints and other factors, and comprehensively evaluate the advantages and disadvantages of these two types of equipment to make the most suitable choice. Only in this way can they improve production efficiency, reduce production costs, improve product quality and enhance the comprehensive competitiveness of enterprises in the market. With the continuous progress and innovation of science and technology, slitting machine technology is also constantly evolving and upgrading. It is expected that these two types of equipment will achieve greater breakthroughs and optimizations in performance in the future, providing more solid technical support for the high-quality development of various industries.